THE FMI STANDARD
The FMI (Functional Mock-up Interface) standard allows system models to be exported in a tool-agnostic format (FMU, or Functional Mock-up Unit). These FMU models can be created by a wide array of 1D/system modeling software tools which can then be integrated into any FMI-compliant simulation toolchain. ThermoAnalytics has developed capabilities both for importing FMU models within CoTherm/TAITherm and exporting an FMU co-simulation interface to TAITherm models.
Using FMI the 1D system models can be combined with TAITherm 3D thermal models, to provide fast and more accurate boundary conditions for the overall simulation process. The 3D TAITherm thermal simulations increase the fidelity of system models by adding detailed thermal effects. This combined approach enables faster and more accurate virtual product development.
Combine TAITherm with FMI and FMU
Connect 3D thermal and 1D system models.
Increase the fidelity of system models by adding detailed thermal effects.
Connecting 3D Thermal and 1D System Models
1D System Models
1D system models are very powerful for early design analysis, but a frequent challenge is modeling complex components that cannot easily be represented through simple correlations or empirical data. To get data for these complex components, engineers can use physical testing or 3D computer-aided engineering models.
3D thermal and 1D dynamic systems
Coupling a 3D thermal and 1D dynamic system models improves the fidelity of both models. The thermal analysis benefits from the detailed fluids prediction performed by the system model, and the system analysis benefits from the high-fidelity heat transfer simulation performed by the 3D model.
FMI-Compliant System Models
TAITherm’s fast transient 3D thermal solver can run thermal models at near real-time speeds, which makes co-simulation practical with 1D dynamic system models. This coupling can be performed using the FMI (Functional Mock-up Interface) system model standard, which allows system models from many different tools to be packaged into a tool-agnostic model format. TAITherm supports exporting or importing FMI-compliant system models (FMUs) that can be co-simulated by a 1D tool, TAITherm, CoTherm, or another system simulation software.
Using FMI to Combine System Models and TAITherm Simulations Webinar
ThermoAnalytics has developed capabilities both for importing FMU models within CoTherm/TAITherm and exporting an FMU co-simulation interface to TAITherm models. This webinar will discuss how FMI capabilities have been implemented around ThermoAnalytics products and will demonstrate example applications for automotive and aerospace industries.
Vehicle Cabin Energy Management
Maximize EV Range
Environmental effects, cabin HVAC efficiency, and battery thermal management are just a few of the variables that contribute to electric vehicle range reduction. To maximize EV range, the vehicle thermal and electrical systems need to be carefully balanced. The vehicle cabin and human occupants have a large energy requirement.
1D and 3D Thermal Co-Simulation Models
1D system tools used with the TAITherm 3D thermal solver support rapid EV cabin studies with improved accuracy for design, analysis, and optimization. 1D and 3D thermal co-simulation models can also be used for the design and testing of control systems from early concept thru system testing.
TAITherm Human Model
The TAITherm Human Thermal model can be included to evaluate localized heating and cooling technologies, heat pumps, thermoelectric generators, and air circulation systems that can improve vehicle designs for shorter passenger time to comfort while reducing energy consumption.
Applications
System Simulation Benefits
A dynamic system model of the fuel system allows the fuel level and fuel fluid properties to be predicted based on the flight scenario, fuel flow rates dictated by the propulsion, return fuel lines, and system components. The end result is a two-way coupled simulation including both high-fidelity heat transfer results and detailed component-level fuel system predictions.
Typical exchange variables would be:
- Fuel level and fuel temperature transferred from the system model to TAITherm
- Heat rates to the fuel and vapor spaces within the tank transferred from TAITherm to the system model
Since both TAITherm and system models can be used to simulate long, dynamic transient scenarios, the approach can be used to virtually evaluate a wide range of flight conditions and test cases.
Simulating Aircraft Fuel Systems
TAITherm’s thermal simulation capabilities allow a comprehensive 3D analysis of aircraft fuel tanks and their thermal interaction with other aircraft systems and the environment. Due to the very different thermal properties of liquid fuel and the air/vapor in the space above the fuel, it is important to consider the fuel level within the tank and its impact on heat transfer to the tank surface.
The fuel level can be modeled either using discrete fuel levels or at a high-resolution local level on the tank surface. Conduction through the tank multi-layer wall is modeled and heat transfer to and from the exterior surface considers radiation, convection, and conduction to adjacent parts or the defined environment (including the effect of the aircraft speed and solar loading).
You Might Be Interested
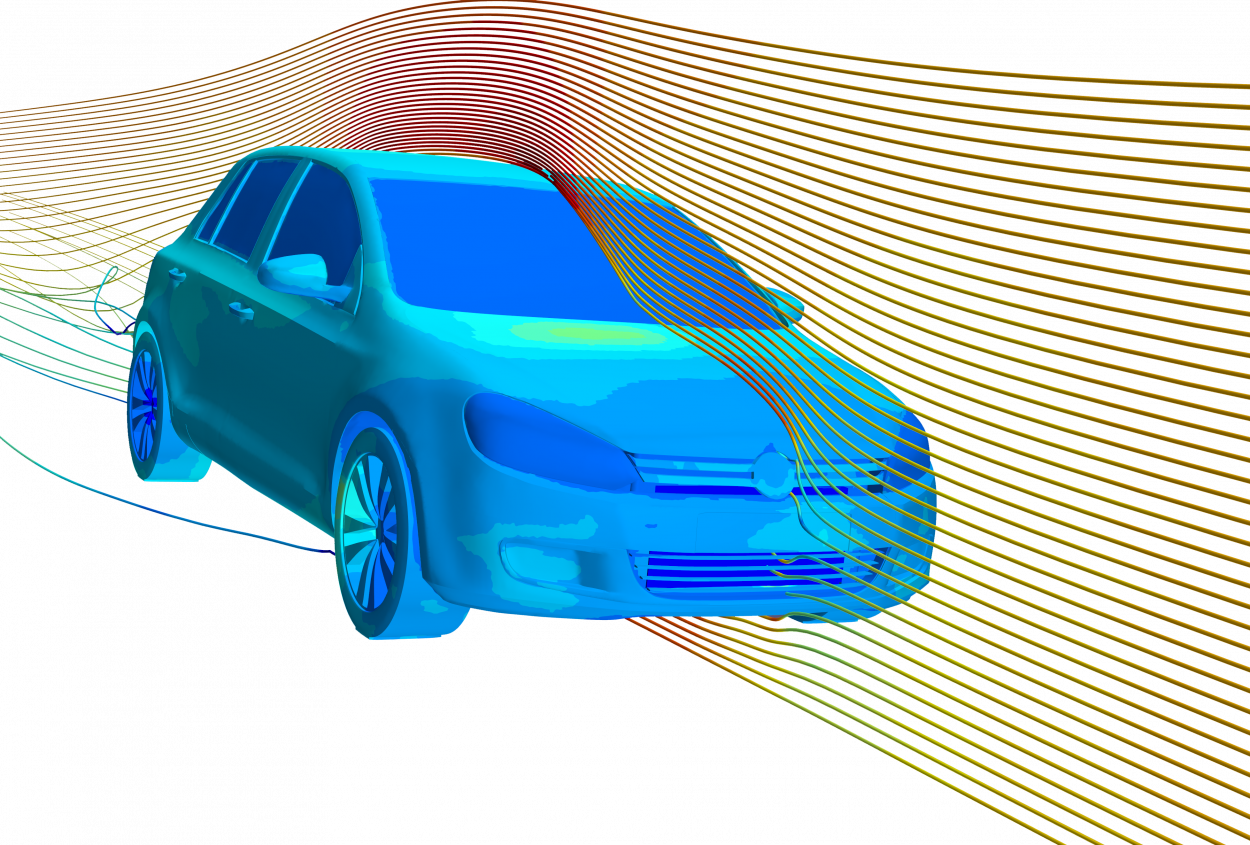
Our custom CAE coupling process allows you to utilize the strengths of multiple simulation tools for better accuracy and in-depth representation of your design problems. Our team is well-versed in TAITherm, our transient thermal simulation tool, and many other popular CAE tools. Resolve your thermal problems quickly and get more time back for optimization when you have us run coupled simulations for you.
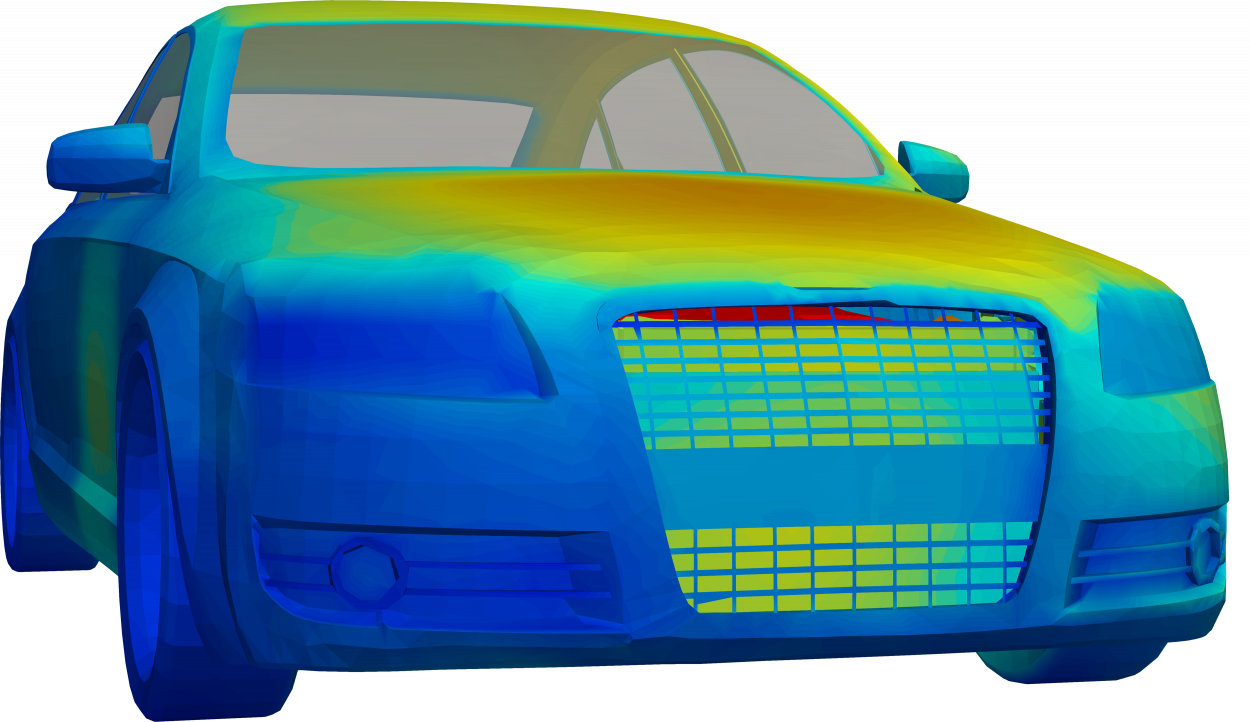
Improve time-to-market & customer satisfaction
With OEMs looking to reduce time-to-market, the ability to save time and resources during product development is crucial.
Traditional methods of designing, building, and testing physical prototypes are costly and time-consuming. Introducing simulation early lets you virtually test your designs for thermal management issues under real-world conditions.
Using TAITherm, our 3D thermal simulation software, you can quickly set up and run steady-state or transient simulations of a full-vehicle model or localized simulations (underhood, underbody, and cabin), with accurate results.
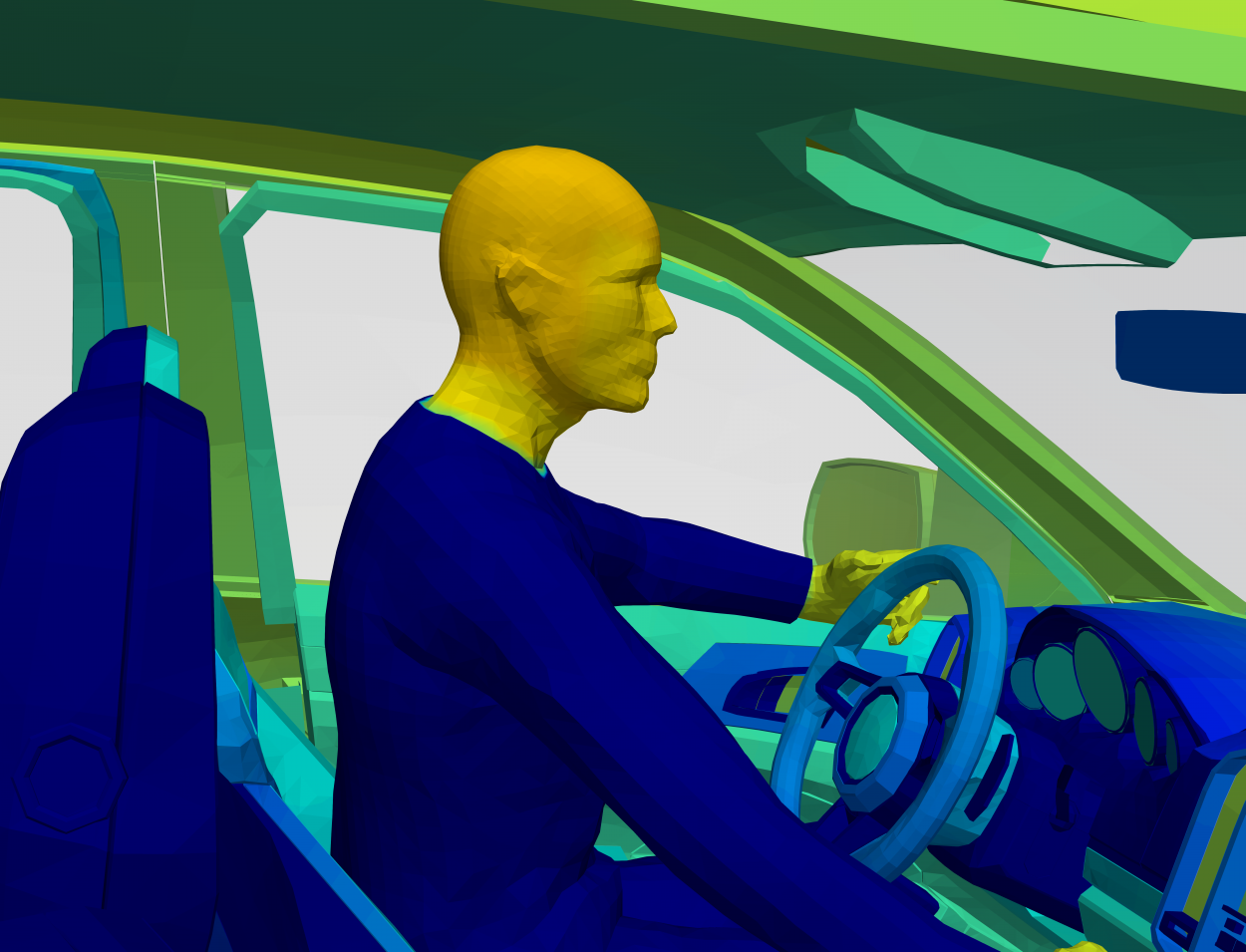
Optimize Occupant Comfort
Because of the time spent in homes, offices, and vehicles traveling between the two, the automotive, architecture, and aerospace industries are all attempting to reach optimal occupant comfort for the utmost satisfaction of their customers. Our expert engineers have the knowledge and skills you need to predict cabin comfort and determine HVAC efficiency for your comfort strategies. They'll help you analyze localized heating and cooling, HVAC systems, and human sensation and comfort to ensure your customer's comfort.